How Cable Manufacturers process order - Understand Ordering Procedure of Cable Industry
In the world of cable manufacturing, we understand that a proper procedure for an order will not only benefit us in speeding up the order confirmation process but also help our clients to follow us through without complication. However, everything has its first time and many of our clients are very new to the industry. In this article, we will go through the order procedure in detail in order to show you how we as a cable manufacturer process orders.
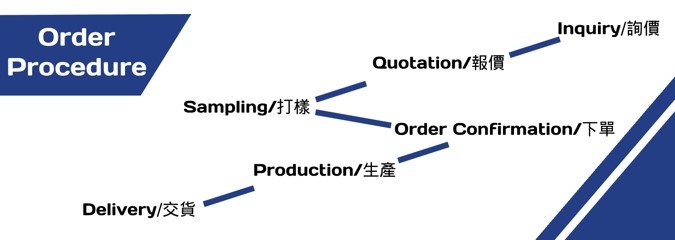
The order procedure can be broken down into 6 steps. Each step takes a different amount of time but it is essential to walk them through step by step or there will be disorganization for both us and the clients which may cost time, resources and even money.
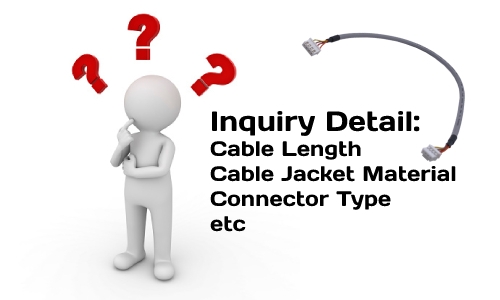
First of all, we need to receive Inquiry. SUNCA is a custom cable manufacturer and exporter especially for B2B business. We will first need to understand what clients need before we can produce. Hence, Inquiry is a crucial step. We will need every single detail about the cable specification from clients. We specifically need information on length, jacket material, connector type, etc for the order. And most importantly, we also need to know the amount of cable product that is needed because it will affect the price greatly. However, SUNCA has one of the lowest MOQ in the cable manufacturing industry and we are able to produce clients' products in little amounts if requirements are met.
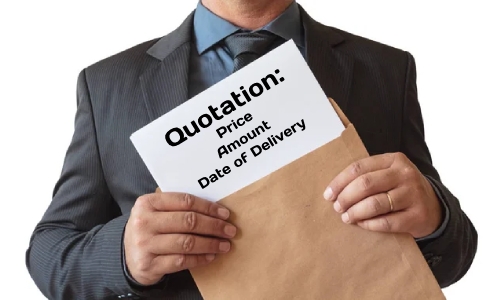
After Inquiry, we will move on to the next step, which is Quotation. In the business of cable manufacturing, quotation has to be the most important part because this is when the clients first time receive pricing and a lot could happen to their decision. Quotation will be sent to clients with details of cable specification and the pricing of the order. If clients are not satisfied with the quotation, we are happy to discuss it with the clients and furthermore understand their needs.
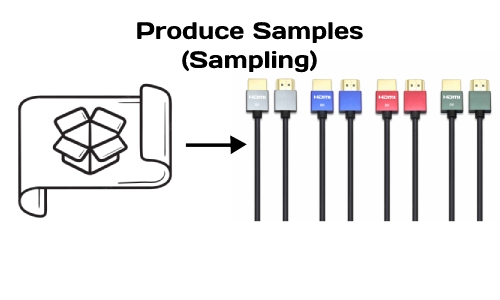
Once both sides have confirmed the quotation, we will start the sampling process. Be aware that the sampling process might not be needed if clients are satisfied with our current available models. Sampling is more likely to be needed when clients have their own custom specification that is unique in the market. It will take roughly 1 week for our factory to produce samples. Once they are fine with the product, we will be able to proceed to the next step.
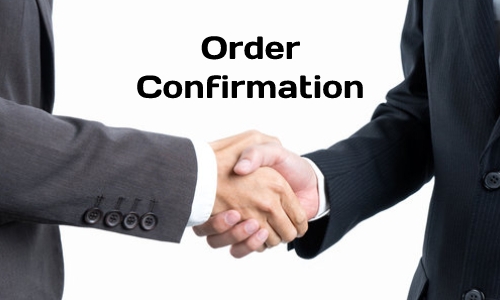
Order Confirmation is the step where clients confirm their required quantity and quotation, etc before we can start mass producing the cables. The process could be quick if clients have no problem with the previous steps. If not, we will have further discussion with clients until we have a common ground.
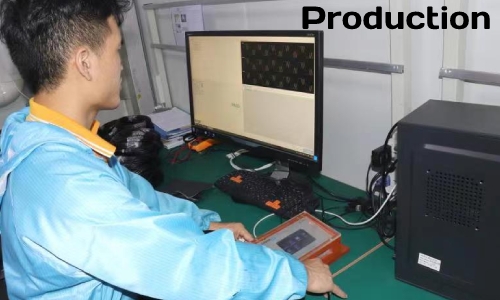
Our cable manufacturing factory will then produce the order for our clients. Depending on many factors such as product amount, cable material, etc, the production time could be varied. However, we will be able to finish production within 3 weeks most of the time.
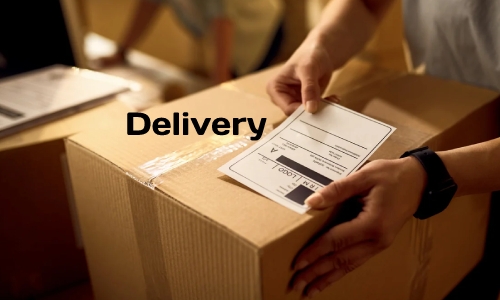
And finally after 1-2 months since the first contact with us, clients will be notified that their orders are on the way to their location. Delivery time is varied depending on the shipping method and shipping companies. After all, We have no control over shipping schedules and pandemic restrictions. But without any complication, the order should be delivered within 5 business days or even in a faster manner.
We hope this information is helpful for you to understand a bit of our order procedure. Be aware that these could be changed due to a lot of different factors and none is 100% absolute. Hence, if you have any questions or concerns on cable manufacturers or manufacturing, feel free to contact us about it! We will be more than happy to answer you!